Hydraulic oil plays a key role in many machine systems, but the phenomenon of oil foaming can be a serious problem. Foaming oil can lead to equipment malfunctions, reduced system performance and a shortened lifespan of hydraulic components. Understanding the causes of this phenomenon is vitally important to maintaining the efficiency and longevity of machinery. It is useful to know what causes hydraulic oil foaming and what measures can be taken to prevent and effectively address the problem.
Causes of foaming of hydraulic oil
It is useful to know what causes hydraulic oil foaming and what measures can be taken to prevent and effectively address the problem.
foaming hydraulic oil – what is foaming and where does it come from?
Foam is a collection of small air bubbles that accumulate on or near the surface of a liquid. In some cases, foam can leak through vents, sight glasses and dipsticks. Foam is an effective thermal insulator, so the temperature of the oil can be hard to control. The presence of air bubbles in the fluid can lead to excessive oxidation, cavitation, deterioration of the lubricating properties of the oil or failure of the hydraulic, lubricating system.
Speaking of hydraulic systems, it is worth noting that the resistance of a lubricant to excessive aeration, which can lead to foaming of the oil, is the result of a reduction in its surface tension. This can be caused primarily by solid contaminants or the presence of water in the oil. Surfactants such as emulsifiers or detergents are added to some lubricants. Their reduction in the oil has the effect of increasing the surface tension, so that the diffusion of air molecules in the oil is impeded, effectively preventing foaming.

Figure: Comparison of the effect of surface tension on foam formation in oil. Mechanism of bubble destruction by the silicone molecule.
why does hydraulic oil foam?
Hydraulic oil foaming is a problem that can occur in hydraulic systems and machinery. There are several main factors that can contribute to this undesirable phenomenon. The most common include:
- poor quality hydraulic oil
- overloading of the hydraulic system
- water pollution
- solid contaminants
- depleted antifouling agent (probably due to intensive filtration processes and electrostatic separation technology)
- cross-mixing of the fluid with an unsuitable lubricant
- too much anti-foam additive – due to incorrect formulation or incorrect reconstitution of the additive package
- lubricant ageing
- defects or leaks in the hydraulic system – mechanical problems causing excessive aeration of the fluid
The causes of hydraulic oil foaming are varied, but often related to the quality of the oil, the load on the system and the condition of the entire hydraulic system. Effective prevention therefore requires careful maintenance, oil quality monitoring and regular servicing to keep the system in optimum condition.
foaming in hydraulic oil – effects of oil foaming
Foaming of hydraulic oil in the context of machine operation and maintenance can lead to a number of negative effects, affecting both operational efficiency and system life. The occurrence of stable foam on the oil surface can worsen the cooling effect and lead to an increase in operating temperature. As a result of increased contact with air, oil oxidation processes are intensified and the oil wears out faster as a result. The operating viscosity may also decrease in some areas, so that the lubricating properties of the oil deteriorate.
Here are some important aspects related to the consequences of this phenomenon:
1. Reduction of Lubricating Properties:
Foaming of the oil affects its lubricating properties, which can result in increased wear on the machine’s working components. A reduction in lubrication efficiency can lead to faster wear of bearings, seals and other components, requiring more frequent repairs and machine downtime. The effect of foam in the oil is also that the oil ages faster and the operating viscosity is reduced.
2. Increase in Oil Temperature:
The process of oil foaming can result in an increase in temperature, which in turn affects the entire hydraulic system. The increased temperature accelerates the wear and degradation processes of the oil, leading to the need for more frequent oil changes and loss of machine efficiency.
3. Reduction in System Performance:
Foaming of hydraulic oil can lead to a reduction in the performance of the entire hydraulic system. Foam formation affects the stability of pressure in the system, which can result in a loss of machine precision and efficiency.
4. Increased Risk of Damage to Hydraulic Components:
Oil foaming increases the risk of cavitation, or air bubbles in the oil, which can lead to damage to pumps, valves and other hydraulic components. This damage can require costly repairs and significantly increase machine downtime.
5. Decrease in Overall Machine Performance:
As a result of all the negative effects of oil foaming, the overall performance of the machine is reduced. This can lead to a loss of operational profitability, increased maintenance costs and the need for more frequent service interventions.
6. Malfunction of Monitoring Sensors
If a layer of foam is present in the oil tank, the sensors monitoring the oil level may present incorrect readings. As a result, the pumps may suck in a mixture of oil and air instead of pure oil. In the hydraulic system, this can lead to cavitation phenomena.
7. Risk of damage to mechanical components:
Foam in bearings prevents the formation of a hydrodynamic lubricating film. A hydrodynamic lubricating film is a layer of oil that forms between the bearing surface and a rotating component, such as a shaft. This oil film acts as a lubricant and surface separator that minimises friction and wear on bearing components.
Foam in bearings interferes with this process by creating gas or air bubbles in the oil film. These bubbles act as a barrier to the formation of a stable hydrodynamic lubricating film, as they interrupt the fluidity of the oil between the bearing surface and the shaft. This means that, in a lubrication system, there is not a sufficient lubricating film layer between the interacting contact surfaces.
8. Risk of fires
Foam on the oil surface can impede heat dissipation from the hydraulic system. In industrial operating conditions, where systems often operate under heavy load, the impeded heat transfer can result in excessive temperature rise and eventually lead to a fire.
what are anti-foaming agents and how do they work?
Anti-foaming agents usually consist of two chemicals: methylsilicone and polymethacrylate. These are mixed with oil in different concentrations depending on the viscosity and other physico-chemical properties of the lubricant in which they are to work. Sometimes the application also influences the type of anti-foaming agent used.
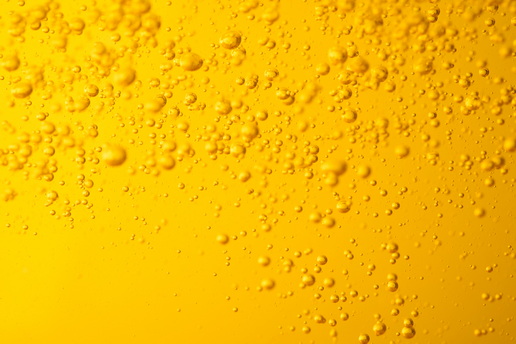
When comparing gear oils to turbine oils, it can be seen that the former are more prone to foaming. This is due to the fact that air bubbles are more likely to be retained in the fluid for longer than in a lower viscosity turbine oil. In turbine oil, air bubbles can float and accumulate on the surface of the fluid more quickly and then disintegrate spontaneously.
Most lubricants contain anti-foam additives to minimise the risk of stable foaming on the oil surface. In order for this agent to fulfil its purpose, there must be a balance between it and other additives in the oil.
The image below shows the principle of this type of additive. When the anti-foaming agent (A) is introduced, it spreads across the surface of the lubricating film, surrounding the bubbles (B). As it spreads, the shear force causes the stabilising film to flow away from the interfacial surface of the gas bubbles, resulting in thinning of the interfacial film (C). Eventually, the bubble bursts (D), releasing the gas it contains.

Figure: Principle of anti-foaming additives.
silicones
Silicones have a very low surface tension of around 21 mNm-¹, which makes them prone to accumulate at the air/oil interface. To be most effective as antifouling agents, they must be insoluble in oil and silicone particles should be smaller than 5 to 7 microns in size to ensure long-lasting performance.
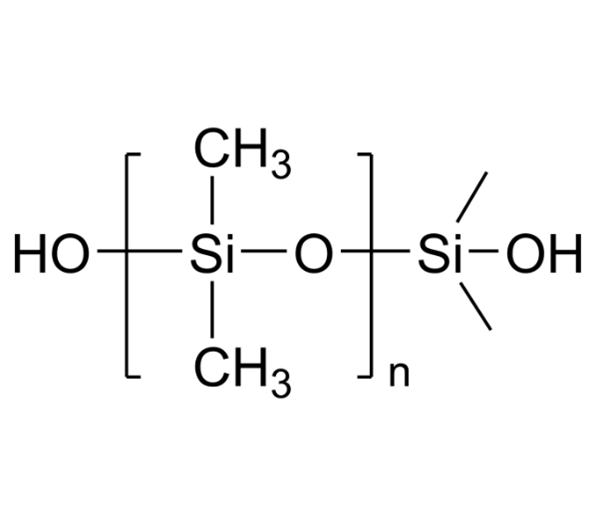
Figure: Chemical structure of polydimethylsiloxane.
acrylic copolymers
Acrylate copolymers are often found in the 0 to 400 ppm range in industrial oils that do not contain detergents or dispersants. They are not as susceptible to air entrainment (air-entrainment) as silicones.
Nonetheless, their excessive addition can lead to excessive aeration, which in turn can result in reactions with other additives. For example, acrylate copolymers have been shown to react with polybutenes, which are commonly used as viscosity index improvers, making them not commonly used in higher viscosity index (VI) oils.
Most studies show no incompatibility between silicone and acrylates, and their effects appear to add up. Antifoam additives based on acrylates can be hypersensitive to contaminants. They can react with polar particles and even with each other to form larger particles called micelles. This makes them less effective, sometimes in as little as six months. Micelles can be broken and the additive can regain its original strength through vigorous mixing. Acrylate copolymers have a completely organic structure and contain no elements other than carbon, oxygen and hydrogen (Figure 2). Consequently, measuring their concentration is not easy, unlike silicone-based antifoam agents, which can be monitored by determining the silicon concentration in new and used oils using atomic emission spectroscopy.
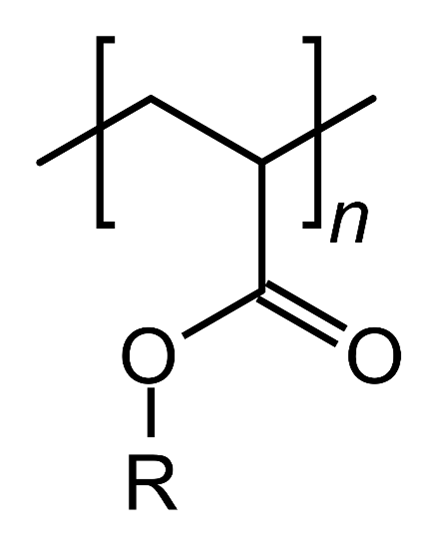
Figure: Chemical structure of the acrylic copolymer.
If the antifoaming agent is silicon-based, it can be monitored by standard elemental analysis of an oil sample. When the silicon level drops, this may indicate that the additive is running out. The best way to monitor organic additives is to carry out performance tests, such as foaming propensity. By comparing these results with new oil, the properties and effectiveness of the additive can be assessed.
Obviously, checking for the presence of foam during the daily inspection of oil level indicators will provide us with a broader picture of potential operating problems. With proper attention and care, antifoam agents can interact effectively with equipment and lubricants. However, we must not forget to select filters appropriately and monitor additive levels regularly to ensure they are working properly.
solutions for foaming in oil – solving the problem
How to remove oil foaming? Solving the problem of foaming hydraulic oil requires a comprehensive approach based on analysis of oil quality, systematic maintenance, monitoring of operating parameters and elimination of potential sources of the problem. These measures, combined with regular maintenance, will maintain the optimal performance of the hydraulic system, eliminating the risk of foaming oil.
By introducing hydraulic oil analysis into the routine maintenance of hydraulic machinery, the risk of oil foaming problems can be effectively minimised, and the performance of the hydraulic system can be monitored and maintained at the highest level.
1. Analysis and Improvement of Oil Quality:
The first step in solving the problem is to carry out a detailed analysis of the quality of the hydraulic oil used. Selecting a high quality oil, free of contaminants and additives, is a key element in eliminating the problem of oil foaming.
2. Oil change (if confirmed by tests):
Oil changes for foaming problems are seen as a last resort rather than a proactive measure. Where research results, and the economics of such action, suggest that the best way to get rid of foaming problems is to change the oil, this solution should be followed.
3. Monitoring of Hydraulic System Parameters:
Constant monitoring of the hydraulic system’s operating parameters, such as temperature, pressure and capacity, allows any deviations to be detected quickly. Reacting to these changes makes it possible to avoid overexposing the oil to foaming conditions.
4. Proper Maintenance and Inspection:
Regular maintenance and servicing can detect possible faults in the hydraulic system. Repairing leaks, damage or replacing worn components effectively eliminates factors that promote oil foaming.
5. Stabilisation of Oil Temperature:
Excessive heating of the oil can accelerate the foaming process. Using appropriate coolers, controlling the system load and maintaining a stable temperature are key aspects in solving the problem.
6. Removal of Air from the System:
Air intake into the lubrication system, associated with leaks, can be one of the factors causing oil foaming. Eliminating any source of air ingress and properly venting the system are key to preventing this problem.
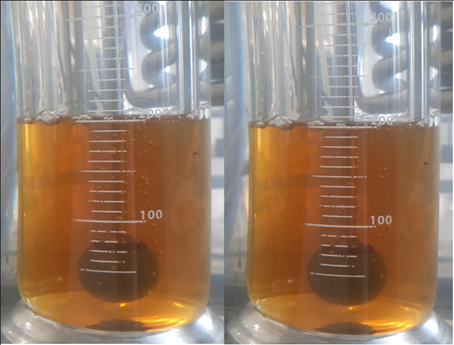
testing the foaming behaviour of oil – test method
The foaming propensity test method is an important tool in analysing and understanding this phenomenon in the context of hydraulic oil and allows a scientific approach to the issue. Find out more
causes of foaming of hydraulic oil
– summary
Knowing the main factors contributing to oil foaming enables informed preventive action to be taken, which in turn contributes to maintaining the efficiency and durability of hydraulic systems.
Equally important is proper prevention, linked to regular testing of the hydraulic oil. Systematic analysis of the oil condition allows early detection of potential problems before they become major faults. Testing the oil makes it possible to monitor its quality, identifying possible contaminants or the presence of foreign substances, which is key to maintaining the optimum performance of a hydraulic machine system.
Regular testing of hydraulic oil provides valuable information on oil consumption, which allows proper planning of oil changes and maintenance of the correct viscosity. Furthermore, by monitoring the chemical parameters of the oil, oxidation or degradation processes can be effectively counteracted, which in turn extends the life of the oil and the entire hydraulic system.
Prevention based on regular hydraulic oil testing not only protects against potential failures, but also contributes to savings by minimising repair costs and keeping machine efficiency at the highest level. Investing in regular hydraulic oil analyses is therefore a key element in the effective care of a hydraulic machine system.
contact
learn more about the diagnostic analysis offerings and how they can benefit your company
Contact our laboratory
Ecol Oil Analysis Laboratory
check also
-
Testing of oils, lubricants, fuels and cooling liquids
Testing services for contaminant levels and physicochemical properties of lubricants, fuels and refrigeration…
-
Oil foaming test method
The foaming propensity test method is an important tool in analysing and understanding…
-
Oil diagnosis and oil change in a hydraulic injection machine
The client detected problems in the operation of one of the hydraulic injection…
-
Analysis of oils and lubricants performed in our laboratory
Recordings and descriptions of oil and lubricant tests performed in our laboratory.